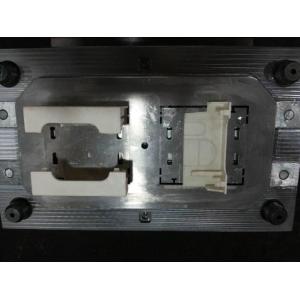
Add to Cart
1. Differences in liquidity
Injection moulding requires high fluidity, especially for thin-walled products and large-scale products. Extrusion requirements are more relaxed, because extrusion is open, there is no huge resistance of reverse die.
2. Melt Strength
Injection moulding is formed in the mold, which has geometric limitations of the mold composition and does not require high melt strength. Although extrusion moulds have geometric limitations, they are not fully solidified after the exit moulds. In this free state, they are sometimes not well formed due to low melt strength (e.g. spinning).
Extrusion is often accompanied by subsequent free state processing, such as hot forming, hollow blow molding, in these forming processes there are often varying degrees of melt tension, if the melt strength is low, it is easy to break. Therefore, injection moulding generally does not require high melt strength, but extrusion is generally required.
3. Export Expansion
Injection moulding generally has no strict requirement for export expansion, and the export expansion of extrusion will cause great problems. Therefore, the viscoelastic control of injection and extrusion materials will be different.
4. Applicable raw materials
Squeeze:
Most thermoplastics and some thermosetting plastics, such as PVC, PS, ABS, PC, PE, PP, PA, acrylic resin, epoxy resin and melamine resin, etc.
Injection Molding:
Except for a few kinds of thermoplastics, almost all thermoplastics can be formed by this method. Injection moulding can also process some thermosetting plastics, such as phenolic plastics.
Characteristic comparison
Extrusion Molding
A. The production process is continuous, and the plastic parts of arbitrary length can be extruded with high production efficiency.
B. The die structure is also simple, easy to manufacture and maintain, less investment and quick effect.
C. The internal structure of the plastic parts is balanced and compact, and the size is stable and accurate.
D. Except fluoroplastics, all thermoplastics can be extruded, and some thermosetting plastics can also be extruded. By changing the die of the machine head, the cross-section shape and size of the product can be changed accordingly, thus various plastic parts of different specifications can be produced.
E. It has wide application range, simple operation equipment, less investment, quick effect, sanitary production environment, low labor intensity, and is suitable for mass production.
injection molding
A. Plastic products of various shapes can be injected and moulded.
B. The structure and dimension of the products are more accurate and the surface quality is better.
C. Injection products can be standardized, standardized and serialized.
D. Simple operation, easy adjustment and renewal of moulding die, fully automatic production can be adopted, high production efficiency;
E. The investment of injection moulding equipment is relatively large, the cost of mould manufacturing is high, and the process conditions of product moulding need to be strictly controlled.